Exploring The Benefits Of Manual Milling
August 13th, 2024, Manual Milling
In the realm of metal fabrication and manufacturing, machining plays a critical role in shaping and producing various components. Among the methods available, manual milling and CNC (Computer Numerical Control) milling are two common techniques. Each approach offers distinct advantages and challenges, making it essential for businesses and individual clients to understand the nuances before deciding which method suits their specific project needs.
Manual Milling vs. CNC Milling
Manual milling involves the direct operation of tools and machines by skilled technicians. This hands-on approach allows for significant flexibility in the machining process, as operators can make adjustments in real-time based on the material’s response and the project requirements. On the other hand, CNC milling relies on computer programming to control the machining tools. The automation CNC offers provides high precision and consistency, making it ideal for large-scale production runs and complex parts.
The selection between manual and CNC milling depends on factors like project scope, complexity, budget, and time constraints. Understanding the capabilities and limitations of each method can empower designers and engineers to make informed decisions that align with practical and design requirements.
Manual Milling: Pros & Cons
Manual milling presents a range of benefits, especially for projects requiring personalized attention.
Advantages of Manual Milling
- Flexibility and Customization: One of the foremost advantages of manual milling is adaptability. Skilled machinists can instantly accommodate for last minute changes or modifications to designs, which a machine would not be able to so quickly understand. This flexibility is particularly advantageous for one-off prototypes or small production runs where each piece may require unique adjustments.
- Cost-Effectiveness for Small Runs: When handling small batches or simple components, manual milling can be less costly. The setup costs associated with CNC machines, such as programming and tooling, may not be advisable for limited production quantities.
- Enhanced Craftsmanship: The tactile nature of manual milling can result in a higher level of craftsmanship. Experienced machinists have a high level of expertise to achieve surfaces and finishes that may sometimes be challenging to replicate with automated processes.
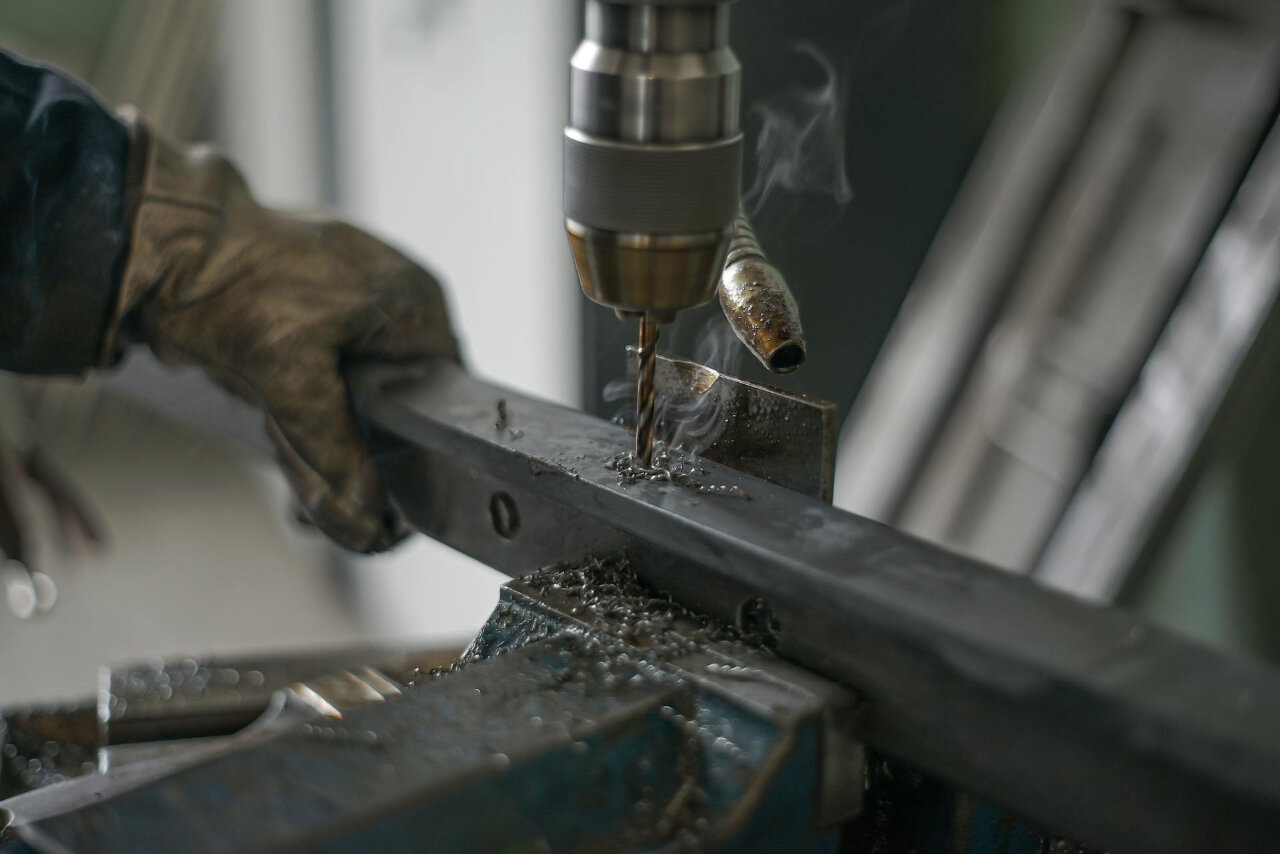
Disadvantages of Manual Milling
- Labor-Intensive: Manual milling typically requires more time and physical effort compared to automated methods. This labor can lead to longer turnaround times, and makes manual milling particularly unfit for large-scale projects.
- Inconsistency in Quality: The variability of human skill levels can introduce inconsistencies in the final product. This can lead to variable factors like restfulness or hunger disrupting the machinist’s precision. While highly skilled machinists are trained to deliver exceptional results despite this, less experienced operators may struggle to achieve the same precision.
- Limited Scalability: As demand increases, scaling manual processes can be challenging. The workforce must proportionately increase, which may not always be feasible for the client.
CNC Milling: Pros & Cons
CNC milling has gained significant popularity in the manufacturing sector, largely due to its automation capabilities and precision.
Advantages of CNC Milling
- High Precision and Reproducibility: CNC milling excels in producing parts with tight tolerances and repeatable accuracy. Once a design is programmed, the machine can produce countless identical units with consistent quality. This makes CNC the ideal choice for mass production.
- Reduced Lead Times: The automation in CNC milling significantly reduces the time from concept to finished product. Complex parts that might take hours or days to fabricate manually are completed in a fraction of the time with CNC.
- Enhanced Safety: With automated processes, CNC milling machines minimize the need for direct human contact with cutting tools during operation, reducing the chances of a workplace hazard or accident.
Disadvantages of CNC Milling
- High Initial Setup Costs: The programming and setup for CNC machines can be costly and time-consuming. For small production runs, these costs may outweigh the benefits, making manual milling more appealing.
- Less Flexibility: Once a CNC program is created, making changes or modifications can be time-consuming and inconvenient.
- Skill Sets Required: While CNC operates with less direct manual input, skilled operators are still necessary to create programs and monitor machine function. This requirement introduces a need for advanced technical knowledge, which may not always be available.
Bring Your Custom Metal Fabrication Project To Life With BSG
At BSG, we understand that choosing between manual and CNC milling is a significant decision that can affect the outcome of your metal fabrication project. Our team of experienced technicians has mastered both techniques, ensuring that we can cater to a diverse range of project needs. We pride ourselves on delivering high-quality metal decorative panels and other custom metal components, no matter the complexity or scale.
Whether you’re looking to create intricate designs with laser cut panels or need precise components for an assembly, our comprehensive capabilities give us the flexibility to adapt to your requirements. We invite you to contact us to discuss your project with our experts. Our team can help determine which machining method is best suited for your specific goals.